Shaping decisions with AI
LTPlabs is a consulting firm that combines Advanced Analytics and AI expertise with a strong business acumen. We’re committed to transforming companies and empower every decision with Analytics.
Answer two questions and put our thinking to work on your challenges
What is your industry?
What are you looking for?
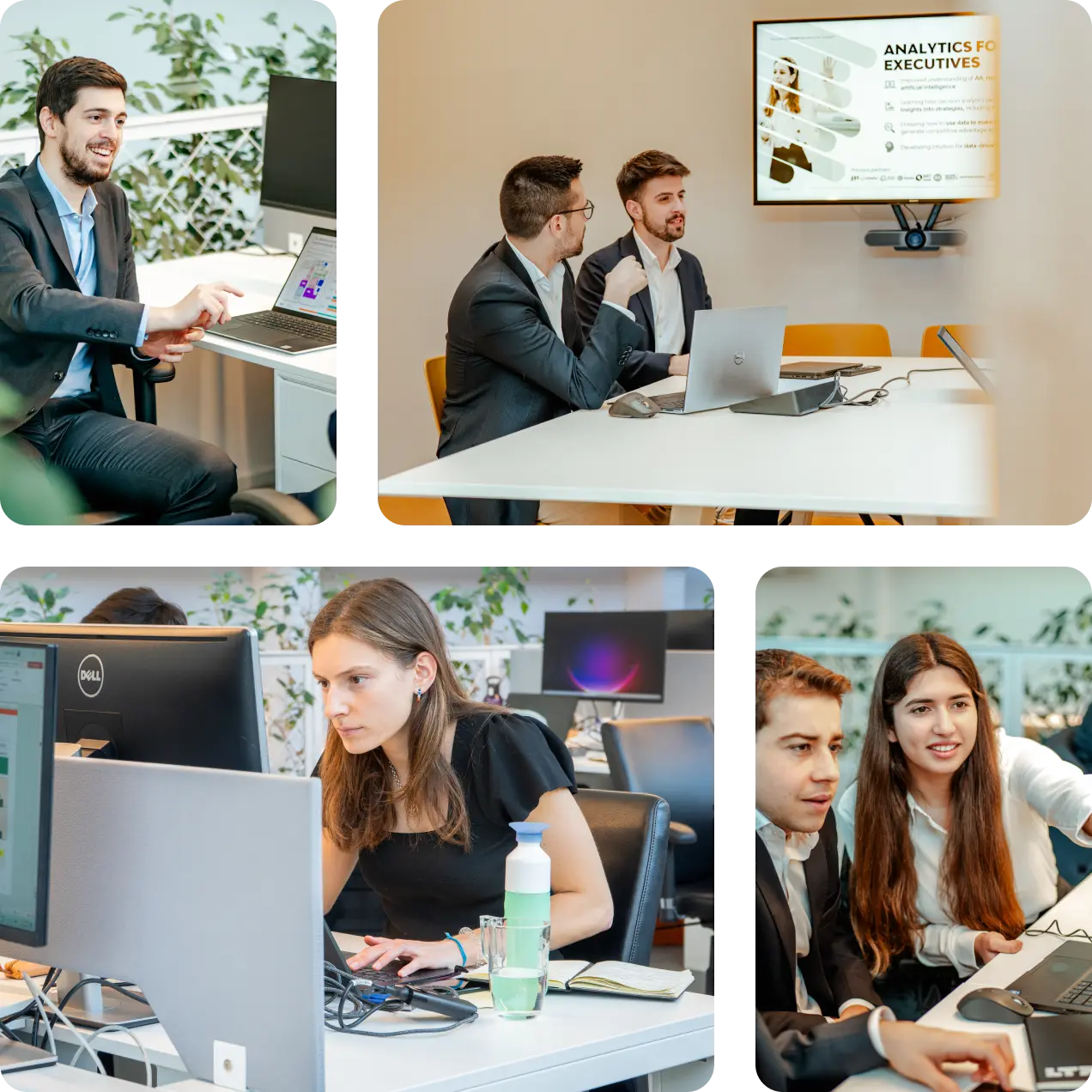
Your partners in AI for Business
Turning data into strategic decisions, driving the future of business with AI.
A solid track-record of transformed businesses worldwide
Our
Impact
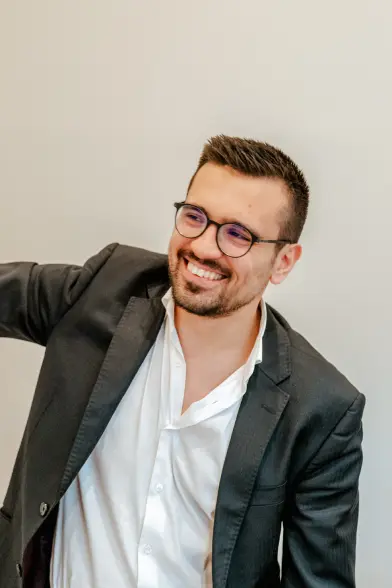
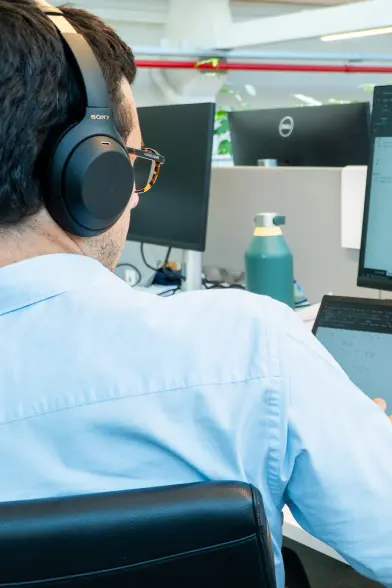
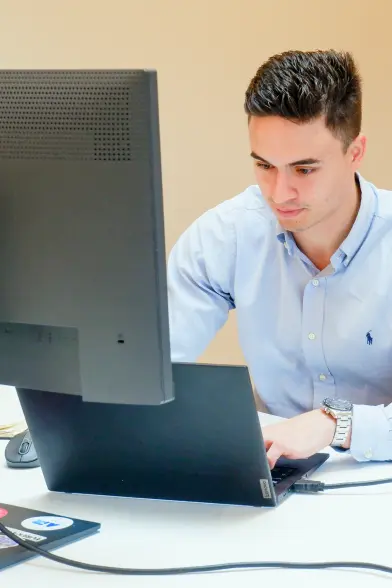
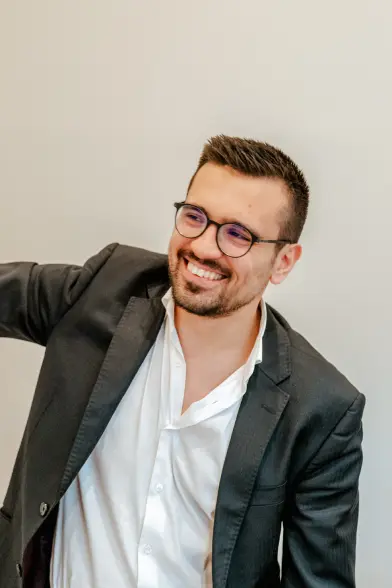
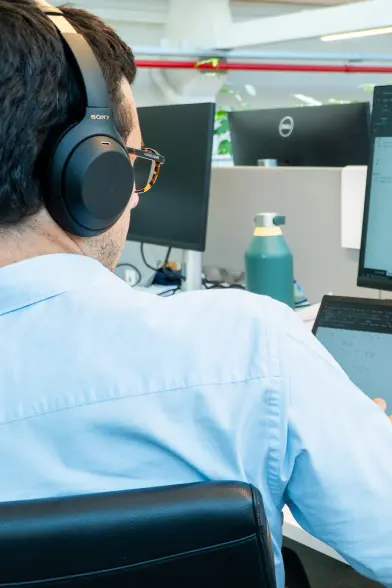
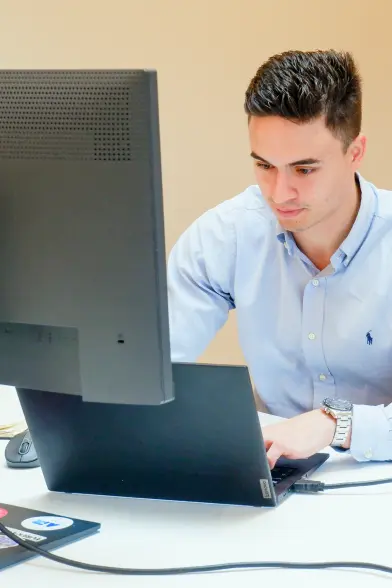
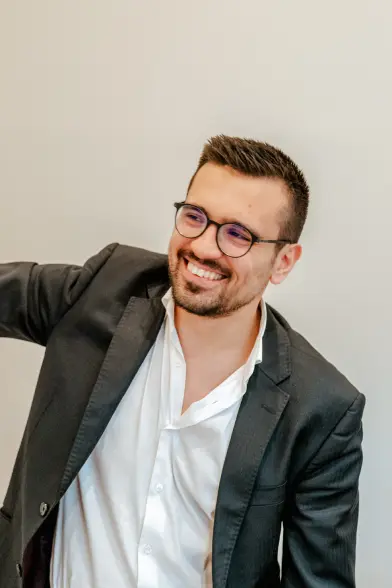
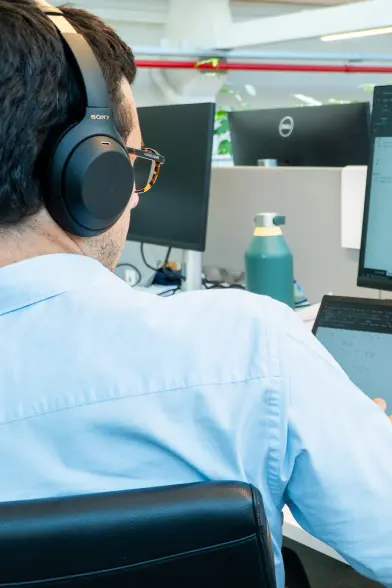
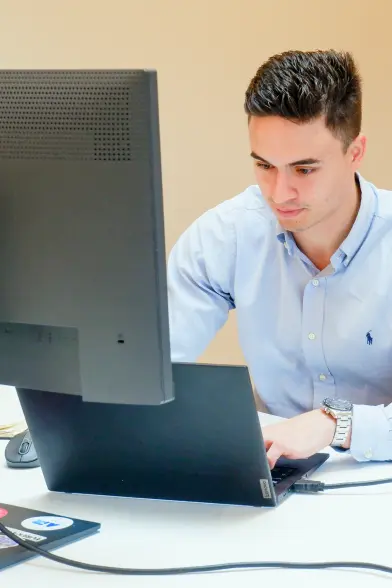
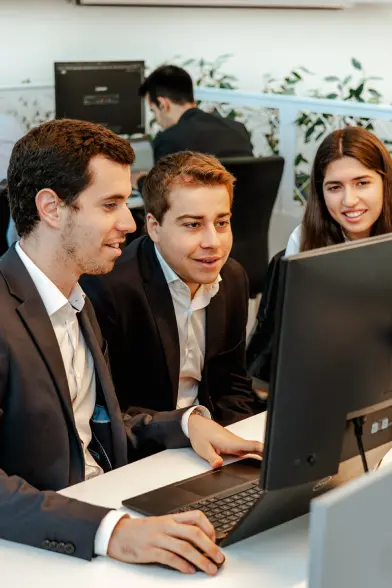
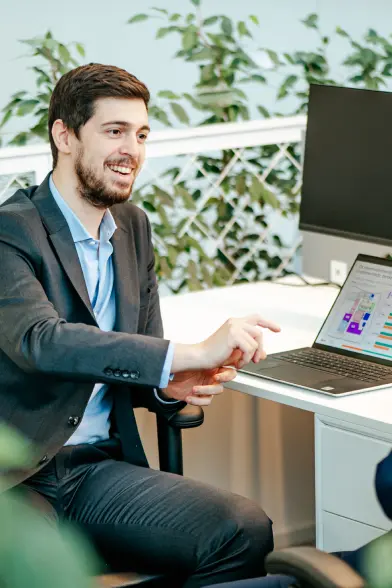
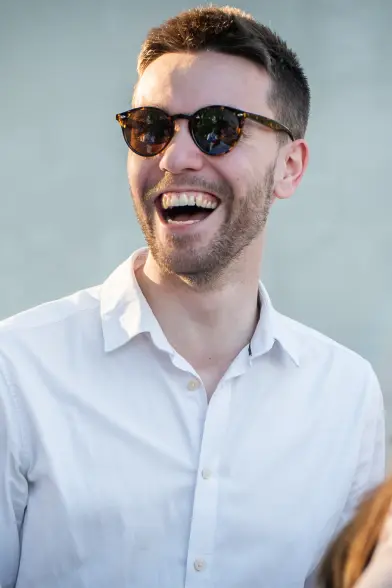
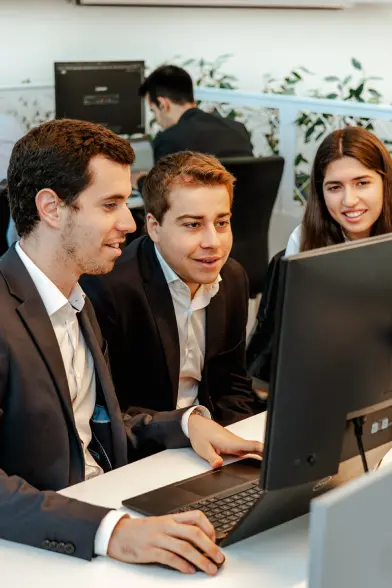
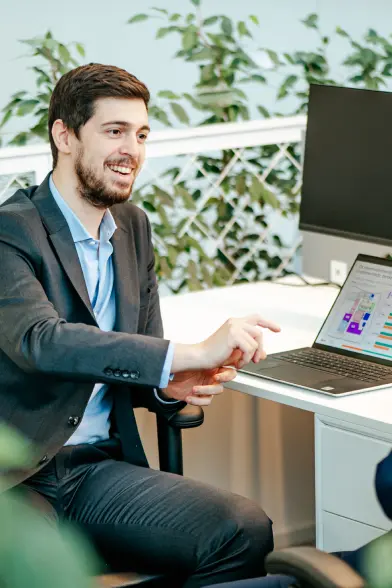
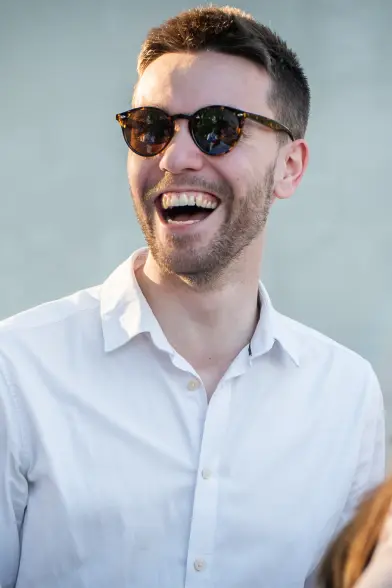
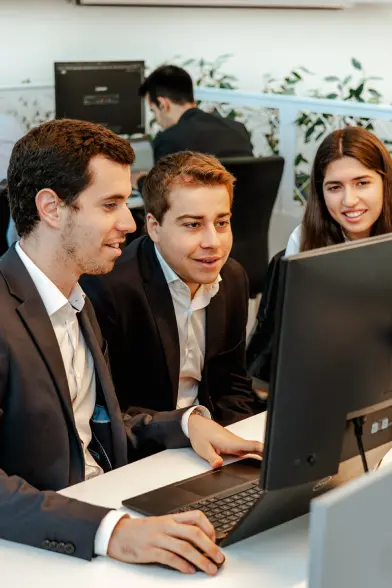
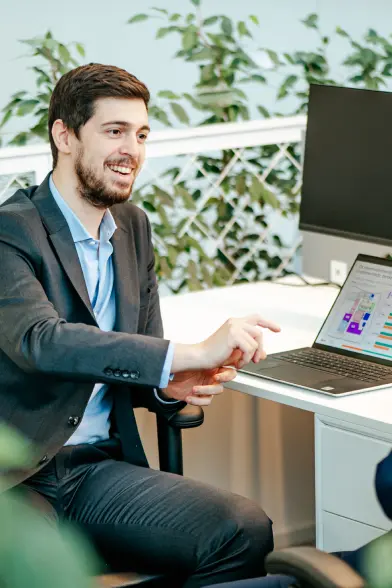
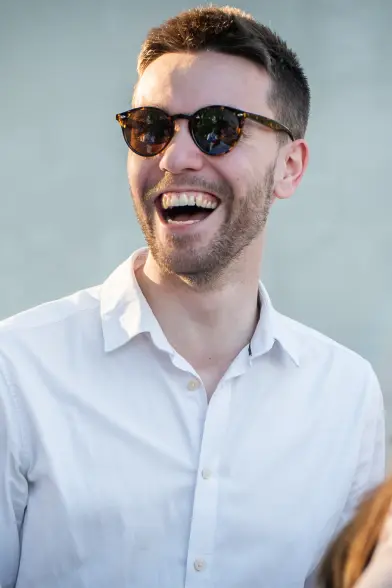
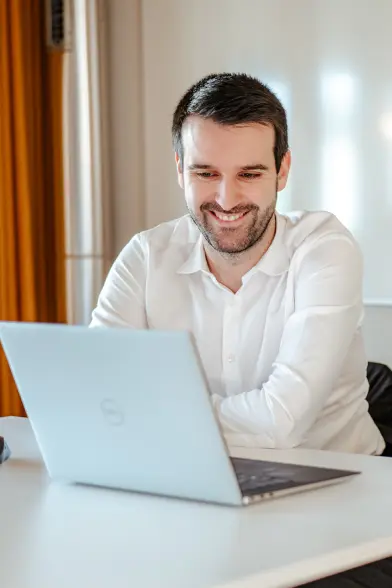
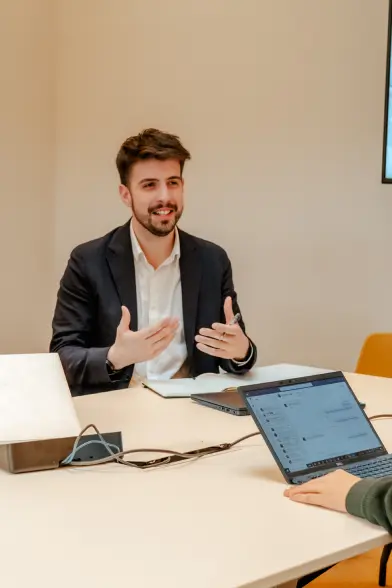
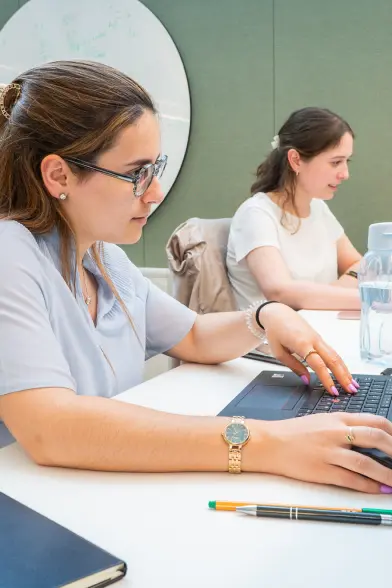
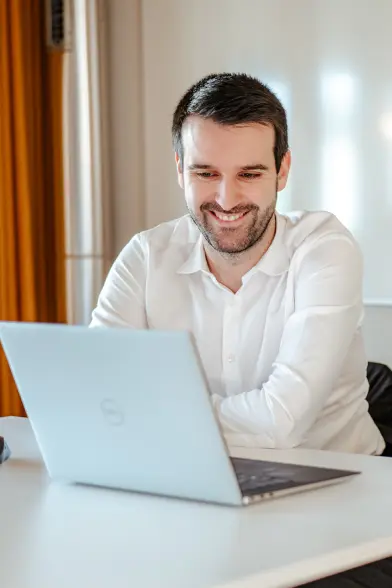
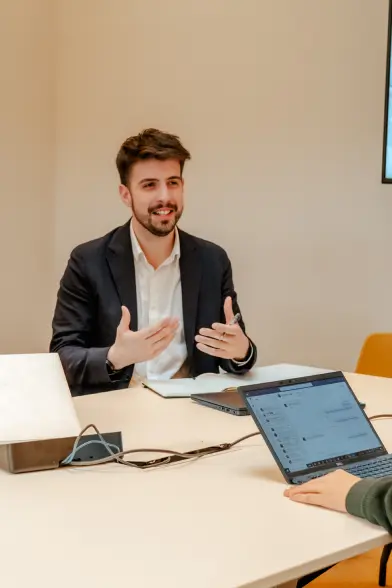
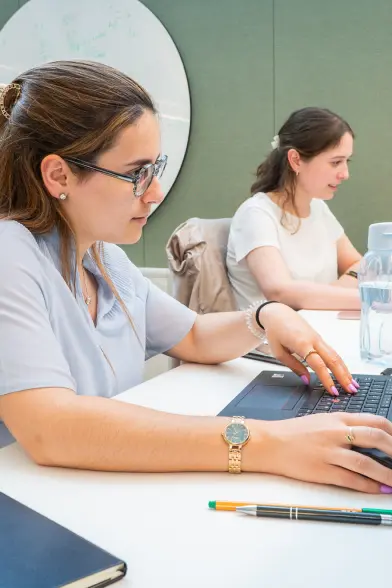
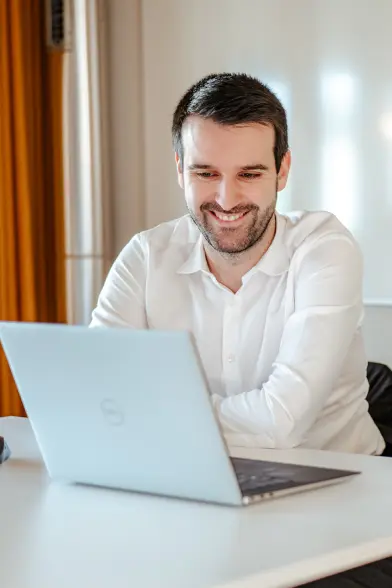
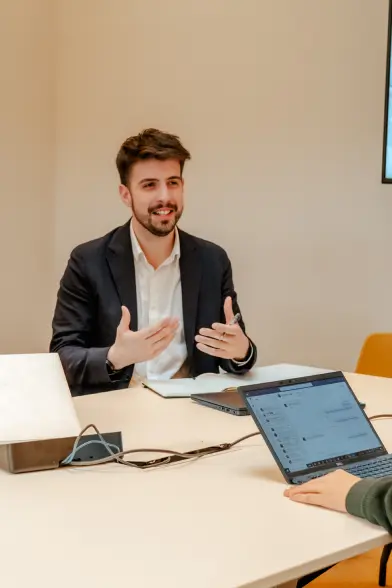
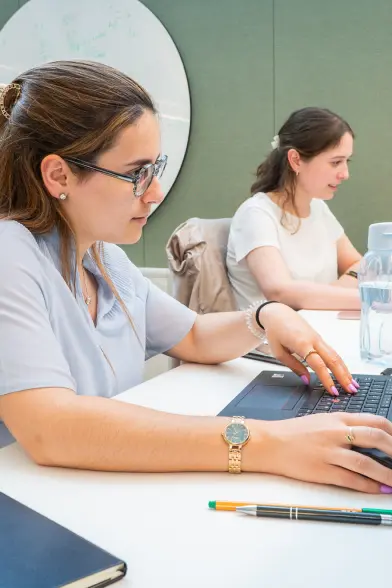